Advantages making difference with other technologies
Points that make our technology superior… ,while ensuring sustainability and environmental awareness.
Amine Absorption Unit and Environment
The hydrogenation reactions produce hydrogen sulfide (H2S), a very harmful substance. Many technologies leave this compound to be removed with the off gases by-products. Others use caustic solution to remove it from the recycle gas. However, treating with caustic produces liquid waste, which is equally dangerous to the environment, it cannot be recycled and will need expensive waste treatment before it can be disposed.
GIT hydrotreating includes an Amine Absorption Unit. The recycle gas is passing through a packed column (absorber), where the H2S is absorbed by a re-circulating counter-current stream of amine solution. The saturated amine solution then is sent to a low pressure column (regenerator), where the H2S is released, so that the cleaned amine is recycled back to the absorber column.
The removal of H2S makes it possible to save hydrogen and achieve a more efficient hydrogenation. The off gases are freed from H2S and can be safely burnt as fuel, while the separated H2S can either be burned in the flare or an incinerator or, in bigger units to be sent to a Claus unit to be converted to solid sulfur, thus contributing to the elimination of the sulfur emissions to environment.
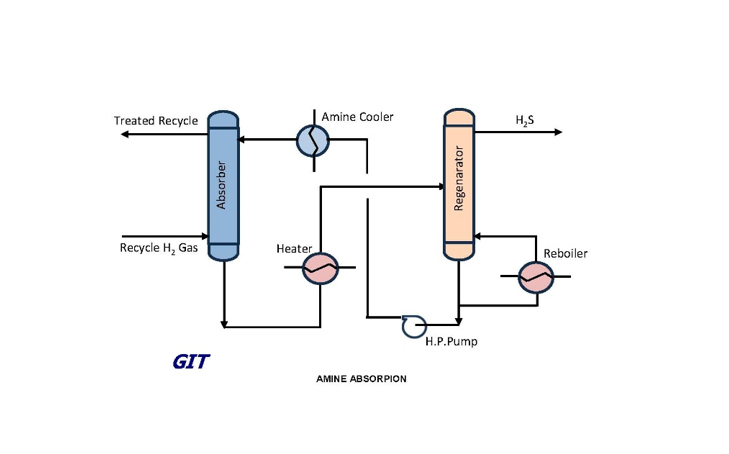
Efficient Hydrogen Recovery
It is important in hydrotreating to minimize the losses of hydrogen. A part of the hydrogen is dissolved in the liquid products after exiting from the reactor and then is removed together with the light off gases in the flash separators, thus lost from the reactor system. The common technic used is to flash the reactor outlet stream in two separators, a high pressure separator and then a low pressure one. Our difference is that we use two high pressure separators, one in high temperature and one in low temperature, following by a low pressure separator. This arrangement achieves a much lower loss of hydrogen, thus lower consumption and in combination with the Amine system we achieve a high recycle hydrogen purity, thus a more effective hydrogenation, best product appearance and less sulfur content.
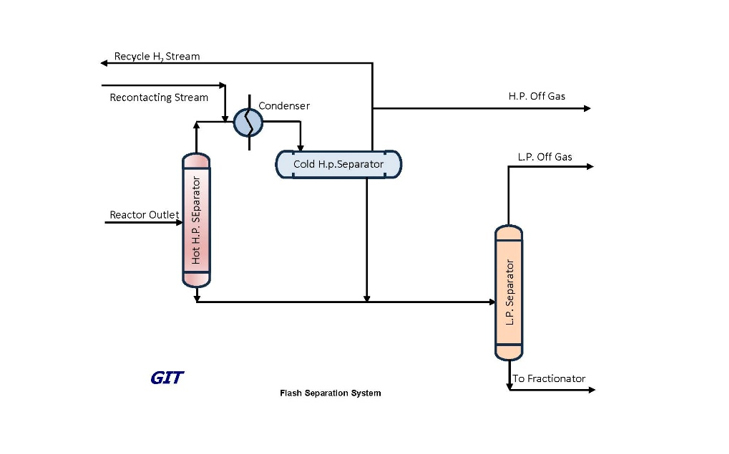
Alternative Re-refining Technologies to meet the different needs of our clients
Re-refining includes two basic steps, first the recovery of the Base Oil Distillates from Used Oil and then follows a finishing step to restore the required specifications. The Hydrotreating process is the way to achieve high quality Base Oils of Group I, II or III. However, there are cases, which need a less expensive solution. GIT is offering its NMP extraction process, for the production of excellent quality Group I Base Oils. The NMP extraction option is an attractive solution, especially for the re-refiner with low capacity in Used Oil feed and who does not need extremely low levels of sulfur in the Base Oils.
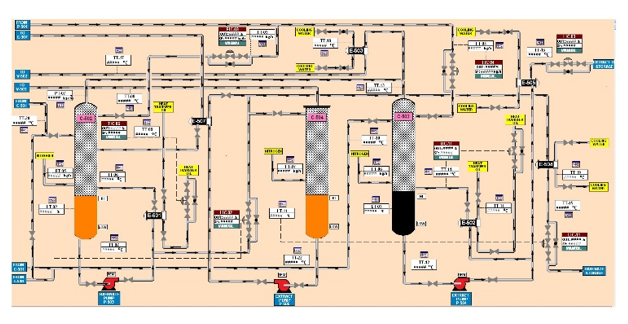
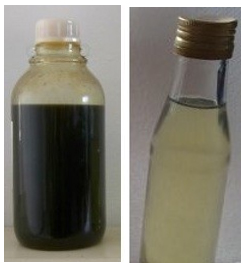
Convert ULO asphaltic vacuum residue to valuable Bright Stock
A large part of the Used Oils from various regions contains heavy base stocks in their formulations. These fractions cannot be recovered even with the most effective vacuum distillation system. They will end up in the vacuum residue, which is a very low value by-product. GIT unique propane extraction process will extract the valuable heavy Bright Stocks from the asphaltic residue, thus effectively boosting the economics of the ULO re-generation process.
Dry Stripping and avoid big quantities of Contaminated Waters
In our Hydrotreater unit as well as in the Solvent extraction, we use our dry stripping process, avoiding the use of stripping steam. This way we avoid production of contaminated water effluents, which need expensive chemical and biological treatment before disposing. The waste treatment needs from the process are eliminated or minimized.
Adapting the hydrotreater unit to each specific case and needs
GIT hydrotreater process is adapted to each specific case, by the suitable design details and catalysts’ selection:
- Used Lube Oils mode, designed for the production of Base Oils, either of Group I or Group II/III.
- Crude oil VGO, for the production of virgin Base Oils either of Group I or Group II
- Diesel range fractions distillates hydrotreater from Used Oils or from Crude Oil
- Production of Ultra Low Sulfur Diesel (ULSD), by deep hydro-desulfurization of Diesel distillates from Crude Oil.
- Re-refining of transformer oils.
- Last but not least, for the small capacity re-refining plants, we have our specially designed “compact” hydrotreater design, which makes hydrotreatment feasible for very small units.
High degree of heat recovery and energy consumption optimization
Care has been taken to recover a big part of the heat of the products, in order to minimize the fuel consumption and the impact on environment. In our bigger hydrotreater units 55% of the required heat comes from the recovery of the heat of the hot products.
Following the international Standards for the design and construction
In our units, we follow the international European and American Standards for the design and construction of our units.
- API
- ASME
- DIN
- NACE
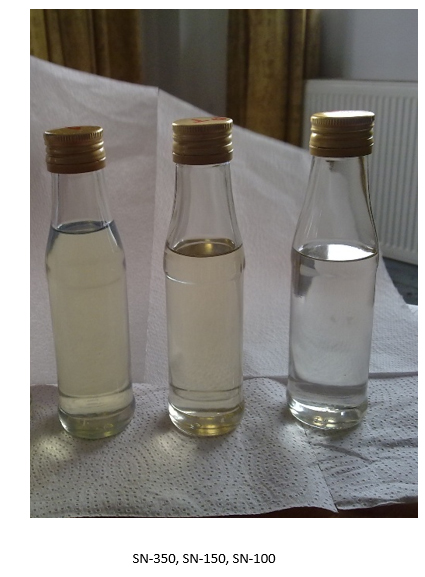