Used Oils Hydrotreating
Our hydrotreating technology of Used Oil Distillates has been specifically designed for the needs of the re-refining industry. The Vacuum Distillates of the Used Oils, first pass through a special thermal treatment and filtering to get rid of substances that will affect the catalyst life, before mixing with hydrogen and preheating. The mixture is passed through a hydrogenation reactor, where there it reacts with hydrogen under high pressure. The chemical reactions include removal of sulphur, nitrogen and chlorine compounds, as well as saturation of unsaturated organic molecules.
The mixture than passes through GIT effective separation section. The gaseous product mixture of the separation section flows through the GIT amine absorption system which makes it possible to maximize the recovery of hydrogen and minimize its consumption. Finally, the liquid product of the separation section is routed to the fractionation section, to be purified.
The result is a product of excellent qualities and stability, water clear color and odorless.
The produced base oil is of Group II+ or Group III level, depending on the nature of feedstock.
The GIT hydrotreater can be designed in different modes to meet the specific requirements;
- High Pressure mode for the production of Group II+/Group III level Base Oils.
- Medium Pressure for the production of Group I base Oils with extremely good color and properties.
- “Compact” mode suitable to be economically feasible for very low capacities.
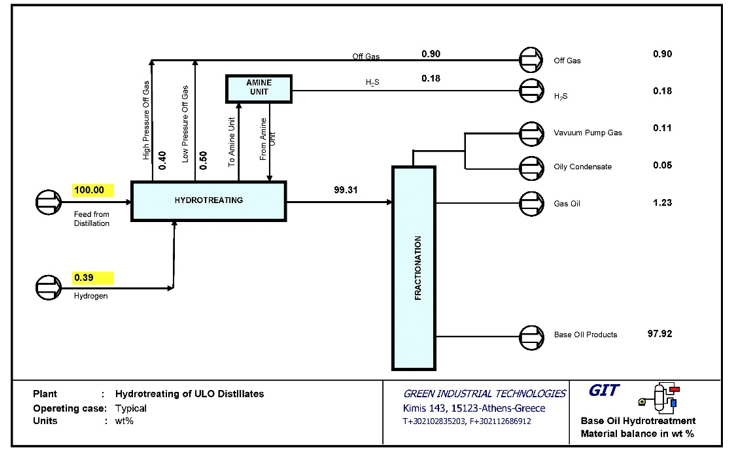
Application: The GIT hydrotreating can accept as raw materials distillates from a wide variety of Used Oils, like car engine oils, marine oils, industrial and hydraulic oils. Also, transformer oils by suitable design.
Consumptions per Metric Ton of distillate feed:
Fuel Oil Equivalent 35 Kg (covered by the unit’s gas and liquid by-products)
Hydrogen Consumption 55 Nm3
Catalysts 0.16 Kg
Hot Oil make up 0.04 Kg
Corrosion Inhibitors 0.06 kg
Power 65 Kwh
Process Water 80 lit
Basic properties of produced Base oils:
VI: 105-125 , depending on the feedstock quality.
Sulfur: 80-150 ppm
Color: <0.5
Unsaturated compounds: <10%
Virgin Base Oils Production
GIT hydrotreating technology, suitably designed, can also be adapted for the production of Base Oils from Crude Oil VGO, after solvent extraction for the aromatics removal and increasing the VI and after Dewaxing in order to fix the desired Pour Point of the products.
The Unit can be designed for the production of Group I or Group II base Oils.
Also, it can be used for the upgrading of Group I base oils to Group II
Production of ULSD
GIT deep hydrotreating technology, can be designed to hydrotreat Diesel range fractions for the production of Ultra Low Sulfur Diesel fuel, with a final Sulfur content of 10 ppm max. The design of the unit is modified in order to be able to hydrotreat lighter fractions, especially the separation and the fractionation section. Also, the reactor design is adjusted for the purpose.
Solvent Extraction for Used Oils Distillates
GIT has its own technology for finishing the Distillates of Used Oils by solvent extraction. The polishing of lube oil distillates is achieved by extraction of the asphaltenes with n‐methyl‐pyrollidone (NMP). The final product is an Excellent quality Group I base Oil.
The extraction is taking place in a packed column, with specifically designed proprietary internals. NMP selectively dissolves the aromatic compounds, such as asphaltenes which give to the lube oil distillate most of its dark color. The treated lube oil distillate (Raffinate) is received from the top of the extraction tower. The asphalt fraction (Extract) is removed from the bottom. Both products are mixed with solvent, which is recovered in the separation section of the unit and recycled. GIT has its proprietary dry extraction technology, which is operating without any contamination of the products with water, thus avoiding the production of contaminated effluents and the necessity of sophisticated water treatment systems.
Application: The GIT solvent extraction can be used instead of hydrotreatment when Base Oils of Group I are required.
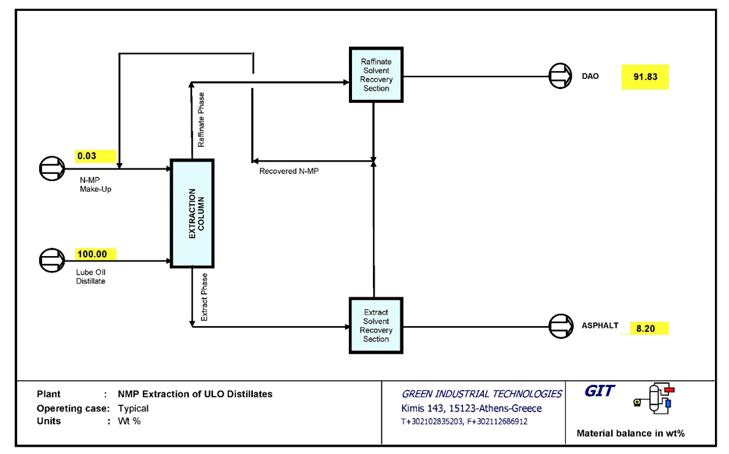
Propane De-asphalting of Vacuum Residue of Used Oils Distillation
Propane De-asphalting is designed for the cases of Used Oils, which contain significant amount of heavy Base oils. Such fractions cannot be recovered by any high vacuum distillation; therefore, they remain in the vacuum distillation residue and compromise the yield of the Base Oils.
The recovery of these heavy fractions is achieved by extraction with liquid propane under pressure. The asphaltenes are removed by the propane extraction process. The remaining product is the de-asphalted oil (DAO) , which after treatment in a finishing unit like hydrotreating, is received as Bright Stock. The yield of Base Oil can be as high as 60% on the vacuum residue, thus increasing the total Base Oils yield and significantly improving the economics of the re-refinery.
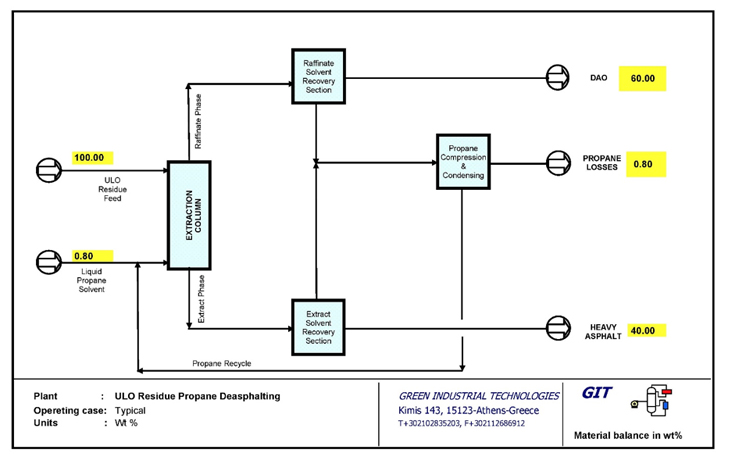
Consumptions per Metric Ton of ULO Residue feed:
Steam : 0.9 tons
Electricity: 55 kwh
Cooling Water Circulation: 85 m3/h
Hot Oil (as heat consumption): 35,000 Kcal
Propane : 8 kg
Properties of DAO:
Density @ 15 °C : 915 Kg/m3
Kinematic Viscosity @ 100 °C : 28-35 cSt (depending on raw material quality)
Acidity (as mg KOH/g): 0.6
Conradson carbon Residue: 0.7 wt%
The product is suitable for hydrotreating to produce Bright Stock.
Properties of final extraction residue:
The final extraction residue is a very heavy product in semi liquid state. Therefore, before the evaporation of propane it is mixed with a small quantity of fluxant material, which can be a part of the distillation residue.
Treatment of Petroleum and Marine waste products
GIT has industrial applications in the area of Oil waste and Marine waste products treatment and recycling. These waste products have widely varying composition and impurities. This makes it necessary to design the process in order to fit each case and to be able to accommodate the different type of the products. GIT process, following the separation of solid contaminants, provides flash separations and distillation in order to separate fractions and produce fuels, which can be used safely as fuel oils of various uses, like as example Marine Fuel Oil.